Manufacturing and Evaluation of Fiber Reinforced Polymer Composites
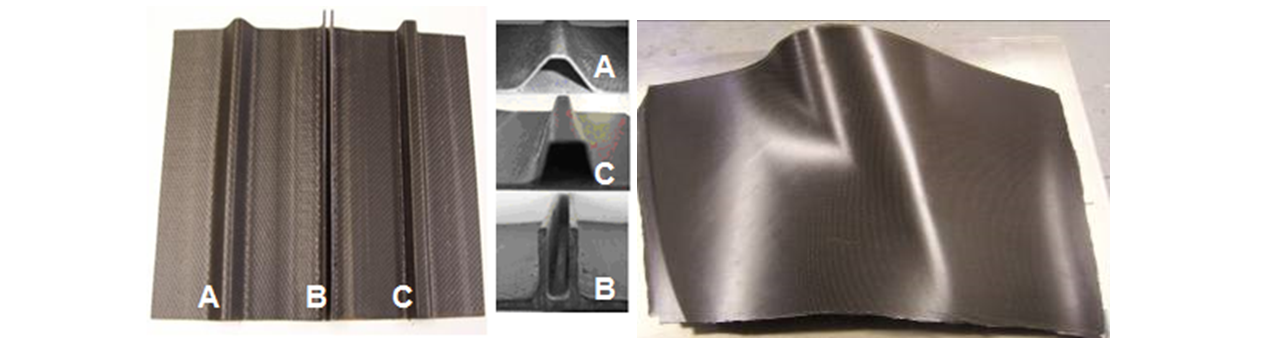
INVESTIGATORS
K. Chandrashekhara (chandra@mst.edu, 573-341-4587), T. Schuman, T. Berkel, D. Pfitzinger, V.G.K. Menta, R. Vuppalapati, G. Dhaliwal and S. Anandan
FUNDING SOURCE
Air Force Research Laboratory, Boeing, Spirit AeroSystems, GKN Aerospace
PROJECT DESCRIPTION
Autoclaves have been commonly used to manufacture high-performance composites for aerospace applications. However, high capital and tooling costs make these composites very expensive. Vacuum-bag-only cure out-of-autoclave (OOA) composite manufacturing process is potentially a lower-cost alternative to autoclave manufacturing. The OOA process does not require the positive pressure of an autoclave but still produces high-quality composite parts. The Out-of-Autoclave (OOA) and Vacuum Assisted Resin Transfer Molding (VARTM) processes will be used to manufacture high-performance composite parts usable in the aerospace industry. Additional quality improvements, cost reductions, and expanded applications are possible through advances in automated infusion, low-cost tooling and bagging concepts, and higher temperature capable resin systems. Composite manufacturing, physical modeling, material characterization, experimental testing and validation with modeling results will be performed for a specific part.
PUBLICATIONS
- “Low-Velocity impact of Composites Manufactured using Out-of-Autoclave Process,” V.G.K. Menta, R. Vuppalapati, K. Chandrashekhara and N. Phan, SAMPE Conference, pp. 1-13, Baltimore, MD, May 18-21, 2009.
- “Out-of-Autoclave Sandwich Structure: Processing Study,” S. Nagarajan, V.G.K. Menta, K. Chandrashekhara, T.R. Berkel, J. Sha, P. Wu, and D. Pfitzinger, SAMPE Journal, Vol. 48, No. 4, pp. 24-31, 2012 (Feature Article).
- “Elevated Temperature Vacuum Assisted Resin Transfer Molding Process for High Performance Aerospace Composites,” V. Menta, R. Vuppalapati, K. Chandrashekhara, T. Schuman, and J. Sha, Polymer International, Vol. 62. pp. 1465-1476, 2013.
- “Manufacturing of Transparent Composites Using Vacuum Infusion Process," Menta, V. G. K., Vuppalapati, R. R., Chandrashekhara, K. and Schuman, T., Polymer & Polymer Composites, Vol. 22, pp. 843 - 850, December 2014.
- “Processing and Performance of Out-of-Autoclave Bismaleimide Composite Sandwich Structures,” S. Anandan, G.S. Dhaliwal, K. Chandrashekhara, T.R. Berkel, and D. Pfitzinger, SAMPE Journal, Vol. 52, No. 3, pp. 44-53, 2016 (Feature Article).
Hydrokinetic Turbine System
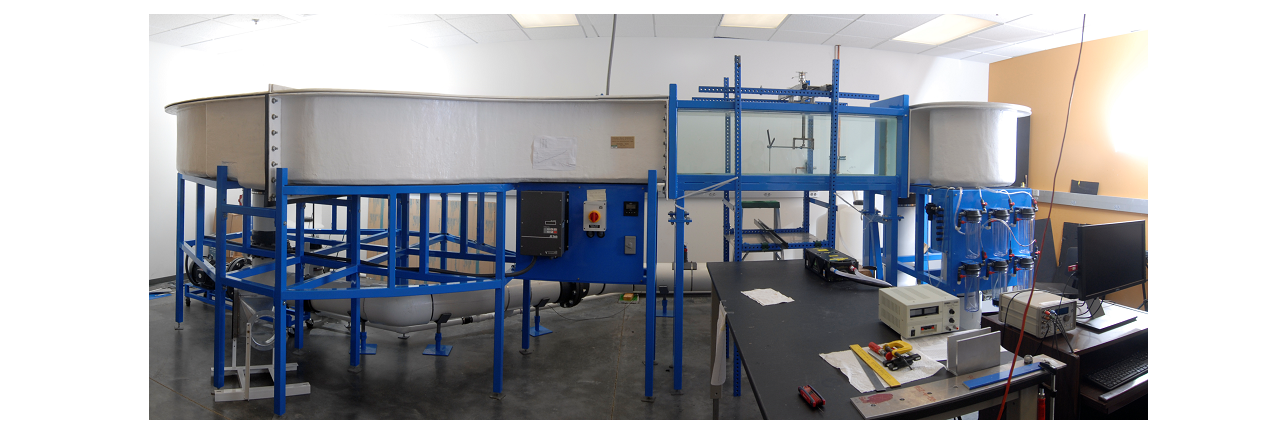
INVESTIGATORS
K. Chandrashekhara (chandra@mst.edu, 573-341-4587), X. Du, J. Rovey, J. Kimball, H. Li, Z. Hu and A. Kashyap
FUNDING SOURCE
Office of Naval Research
PROJECT DESCRIPTION
Hydrokinetic system with metallic and composite blades were developed in Missouri S&T. The water tunnel facility at Missouri S&T was used to study the system-level performance of the hydropower system. All components such as turbine blades, duct and diffuser, power train, and electric interface were manufactured in-house. The system was evaluated in terms of power generation, structural performance and system efficiency. Current investigation includes the effect of varying pitch angle of the rotor on the system efficiency. Effects of flow velocity and rotational speed of the rotor, are also being investigated. The use of co-axial turbine systems for power generation is another area of research at Missouri S&T. The results from experimental testing are used to validate CFD simulations.
PUBLICATIONS
- “Structural Health Monitoring Data Transmission for Composite Hydrokinetic Turbine Blades,” Heckman, J.L. Rovey, K. Chandrashekhara, S.E. Watkins, D.S. Stutts, A. Banerjee, and R.S. Mishra, Advanced Shipping and Ocean Engineering, Vol. 12, No. 2, pp. 50-59, 2013.
- “Simulation-Based Time-Dependent Reliability Analysis for Composite Hydrokinetic Turbine Blades,” Z. Hu, H. Li, X. Du, X, and K. Chandrashekhara, Structural and Multidisciplinary Optimization, Vol. 47, pp. 765-781, May 2013.
- "Reliability–Based Fatigue Life Investigation for a Medium-Scale Composite Hydrokinetic Turbine Blade," Li, H., Hu, Z., Chandrashekhara, K., Du, X. and Mishra, R., Ocean Engineering, Vol. 89, pp. 230 - 242, October 1, 2014.
- "Particle Swarm-Based Structural Optimization of Laminated Composite Hydrokinetic Turbine Blades," Li, H. and Chandrashekhara, K., Engineering Optimization, Vol. 47, No. 9, pp. 1191 - 1207, June 2015.
- “Design and Performance Evaluation of a Horizontal Axis Hydrokinetic Turbine System,” H. Li, G. A. Taylor, A. M. Abutunis, K. Chandrashekhara, A. R. Kashyap and J. W. Kimball Paper Number 3166, pp. 1-15, Proceedings of the Society for the Advancement of Material and Process Engineering (SAMPE) Conference, Long Beach, CA, May 6-9, 2013.
Bio-composite Panels for Energy Efficient Housing
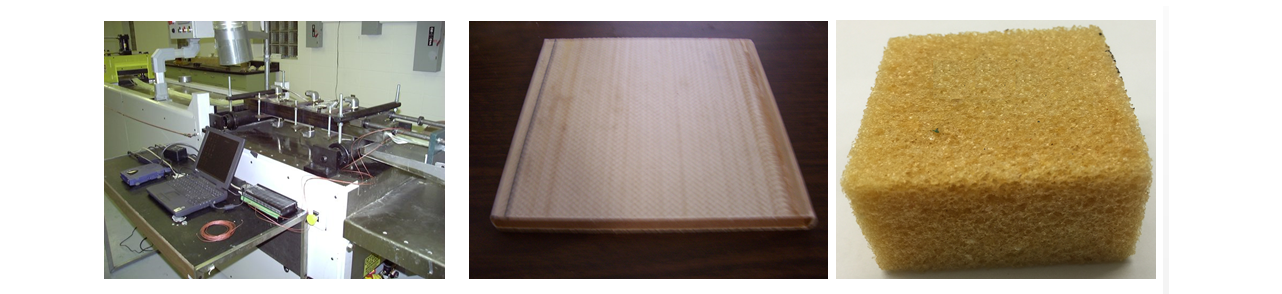
INVESTIGATORS
K. Chandrashekhara (chandra@mst.edu, 573-341-4587), T. Schuman, P. Nam, A. Shabeer, G. Liang, S. Sundararaman, S. Anandan and G. Dhaliwal
FUNDING SOURCE
National Science Foundation, United Soybean Board and Missouri Soybean Merchandising Council
PROJECT DESCRIPTION
The goal of the proposed research is to use bio-based composites for panelized housing construction which will improve durability, energy efficiency, structural performance, fire resistance and affordability of houses. The research will focus on the application of renewable materials to develop core-filled multifunctional composite panels for housing. The following primary tasks will be investigated: Manufacturing of integral core-filled pultruded panels for floor, roof and wall using renewable raw materials; Experimental testing and simulation to evaluate the performance of the core-filled panels; Design of connections for panelized housing construction; Construction of a prototype house and energy efficiency evaluation. High performance panels will be manufactured using an innovative integral core-filled pultrusion process. Soy resin, soy foam and natural fibers will be used as raw materials and will provide better impact resistance and insulation. Glass fibers will be used for outer layer to provide additional stiffness and strength. Nano-silica recovered from rice hull will be added during the pultrusion process to enhance the fire resistance capability of these new materials. The core-filled panels will be tested under different loading and environmental conditions. Experimental results will be compared with finite element solutions.
PUBLICATIONS
- “Cure Kinetics and Rheology Characterization of Soy-based Epoxy Resin System,” G. Liang and K. Chandrashekhara, Journal of Applied Polymer Science, Vol. 102, pp. 3168-3180, 2006.
- “Synthesis and Characterization of Soy-based Nanocomposites,” A. Shabeer, K. Chandrashekhara and T. Schuman, Journal of Composite Materials, Vol. 41, No. 15, pp. 1825-1850, 2007.
- “Impact Behavior of Fiber Reinforced Pultruded Soy-Epoxy Composites,” S. Sundararaman, A. Shabeer, K. Chandrashekhara and T. Schuman, Journal of Biobased Materials and Bioenergy, Vol. 2, pp. 1-7, 2008.
- “Core-filled Biocomposite Panels for Energy Efficient Housing,” K. Chandrashekhara and W.E. Showalter, Proceedings of NSF CMMI Engineering Research and Innovation Conference, pp. 1-10, Knoxville, TN, January 7-10, 2008
- “Neural Network Based Constitutive Model for Elastomeric Foam,” G. Liang and K. Chandrashekhara, Engineering Structures , Vol. 30, pp. 2002-2011, 2008.
- "Manufacturing and Impact Characterization of Soy-Based Polyurethane Pultruded Composites," R. Vuppalapati, V.G.K. Menta, K. Chandrashekhara, and T. Schuman, Polymer Composites, Vol. 35, pp. 1070 - 1077, June 2014.
- "Manufacturing and Performance Evaluation of Polyurethane Composites Using One-Part and Two-Part Resin Systems," M. Mohamed, S. Hawkins, and K. Chandrashekhara, Polymers & Polymer Composites, Vol. 23, No. 5, pp. 333 - 344, 2015.
- "Fabrication and Testing of Soy-based PU Foam," G.S. Dhaliwal, S. Anandan, N. Dudenhoeffer, P. Nam and K. Chandrashekhara, Composites and Advanced Materials Expo (CAMX) Conference, Paper No. 0148, Anaheim CA, September 26 - 29, 2016.
Modeling and Finite Element Simulation

INVESTIGATORS
K. Chandrashekhara (chandra@mst.edu, 573-341-4587), J. Hu, S. Sundararaman, V. Bheemreddy, H. Li and J. Chen
FUNDING SOURCE
Army Research Lab, Department of Transportation, Bell Helicopter and Mark IV Automotive
PROJECT DESCRIPTION
Numerical modeling and simulations are cost effective alternatives in-situ experimental and statistical means of studying the behavior of structures. A parametric experimental study can be very complex to set-up, time consuming to execute and can requires expensive raw materials. Researchers at Missouri S&T built a comprehensive numerical model which can be used to design a V-ribbed belt drive system. The study of belt drive mechanical performance is fairly complicated due to several nonlinearities: material nonlinearity from the belt rubber compound, geometrical nonlinearity from the large deformation of belt, and boundary nonlinearity from the belt and pulley sliding motion. Nonlinear material models were built to predict such behavior. Composite curing and optimization of process parameters was another area of research. The cure kinetics of composite parts is particularly difficult to model when tool/part geometries are complex. A general-purpose, finite-element package with multiphysics capabilities was used for simulating the non-isothermal cavity molding process. Multiscale and Multiphysics modeling of hot radial forging process was also performed at Missouri S&T.
PUBLICATIONS
- “Finite Element Analysis of V-Ribbed Belt/Pulley System with Pulley Misalignment using a Neural Network based Material Model,” J. Hu, J. Chen, S. Sundararaman and K. Chandrashekhara, Neural Computing and Applications, Vol. 18, pp. 927-938, 2009.
- “Thermal Fatigue-Failure Analysis of V-ribbed Serpentine Belts,” S. Sundararaman, J. Hu, J. Chen and K. Chandrashekhara, International Journal of Fatigue, Vol. 31, pp. 1262-1270, 2009.
- “Failure Analysis of Hydrogen Storage Composite Cylinders with Liner Crack accounting for Autofrettage Effect,” J. Hu and K. Chandrashekhara, International Journal of Hydrogen Energy, Vol. 34, pp. 3425-3435, 2009.
- “Study of Void Closure in Hot Radial Forging Process Using 3D Nonlinear Finite Element Analysis”, J. Chen, K. Chandrashekhara, C. Mahimkar, S. N. Lekakh and V. L. Richards, International Journal of Advanced Manufacturing Technology, Vol. 62, pp.1001-1011, 2012.
- “Modeling of Fiber Pull-Out in Continuous Fiber Reinforced Ceramic Composites using Finite Element Method and Artificial Neural Networks,” V. Bheemreddy, K. Chandrashekhara, L. R. Dharani, and G. E. Hilmas,Computational Materials Science, Vol. 79, pp. 663-673, 2013.
- "Modeling and Characterization of Fused Deposition Modeling Tooling for Vacuum Assisted Resin Transfer Molding Process," Li, H., Taylor, G., Bheemreddy, V., Iyibilgin, O., Leu, M. and Chandrashekhara, K., Additive Manufacturing, Vol. 7, pp. 64 - 72, July 2015.
- “Modeling and Simulation of Cure Kinetics and Flow in Cavity-Molded Composites,” Bheemreddy, V., Huo, Z., Chandrashekhara, K., and Brack, R.A., Journal of the American Helicopter Society, Vol. 61, pp. 022004-1-022004-10, 2016.
Follow Intelligent Systems Center