Improving the Machinability of Difficult-to-cut Metals in High Speed End-milling
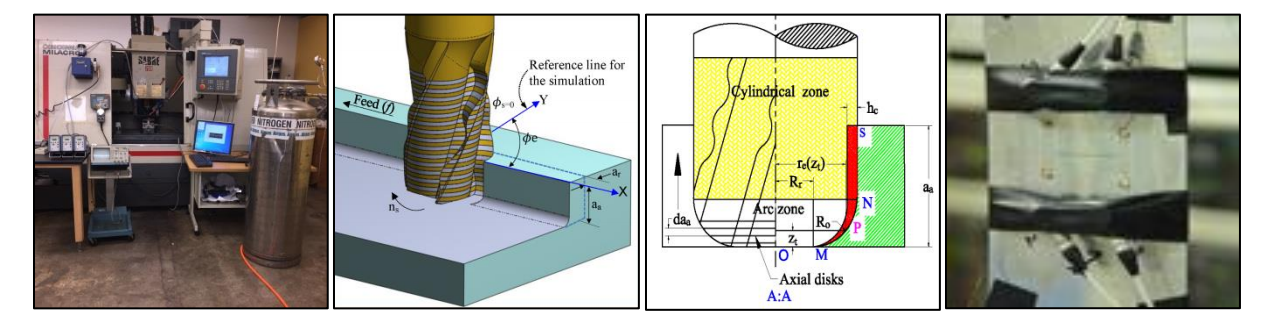
INVESTIGATORS
Dr. Anthony C. Okafor (okafor@mst.edu, (573) 341-4695)
FUNDING SOURCE
National Science Foundation, Air Force Research Laboratory, Office of Naval Research
PROJECT DESCRIPTION
This research develops mechanistic cutting force model for wavy-edged/bull-nose helical end-mills, and procedure for predicting cutting force components. This research also investigates the effects of multiple cooling strategies and machining parameters on machinability of difficult-to-cut metals using high speed machining and wavy-edge/bull-nose helical end-mills. The machinability parameters investigated include: Cutting force components, Surface roughness, Residual stresses, Cutting temperature, and Tool wear. The objectives were achieved by performing 1) Design and assemble a cryogenic flow line, 2) Design and assemble a nozzle to deliver minimum quantity lubrication to the cutting zone, 3) Calibration of cryogenic liquid nitrogen flow against cold air, 4) machining experiments to investigate the effects of cooling strategies on machinability of titanium alloy, 5) machining experiments to investigate the effects of cooling strategies on machinability of Inconel alloy, 6) investigate the effects of cooling strategies on residual stresses, 7) Machining experiments to determine specific cutting and edge force coefficients (Ktc, Krc, Kac Kte, Kre, Kae) for each cooling strategy, 8) Development of mechanistic cutting force model for bull-nose/wavy-edge end-mills; 9) Development of MATLAB code for simulation of cutting forces, and 10) Experimental validation.
PUBLICATIONS
- “Effects of Geometric Parameters of Wavy-edge Bull-nose Helical End-mill on Cutting Force Prediction in End-Milling of Inconel 718 under MQL Cooling Strategy,” Abdulhakim Ali Sultan, A. Chukwujekwu Okafor, Journal of Manufacturing Processes, Vol. 23 (2016), pp 102-114,
- “Development of a Mechanistic Cutting Force Model for Wavy-edge Bull-nose Helical End-milling of Inconel 718 under Emulsion Cooling Strategy,” A. Chukwujekwu Okafor and Abdulhakim Ali Sultan, Applied Mathematical Modeling, Vol. 40, (2016), pp 2637-2660.
- “Acoustic Emission Detection and Prediction of Fatigue Crack Propagation in Composite Patch Repairs Using Neural Network,” A. Chukwujekwu Okafor, Navdeep Singh, Navrag Singh and Benjamin N Oguejiofor, Journal of Thermoplastic Composite Materials, Vol. 28, No. 22, pp 1-27, June 2015, also DOI 10.1177/0892705715573649, March 4, 2015, jtc.sagepub.com.
- “Evaluation of the Effects of Corrosion on Fatigue Life of Clad Aluminum Alloy 2024-T3 Riveted Lap Joints with Acoustic Emission Monitoring,” A. Chukwujekwu Okafor and Christopher Nnadili, Journal of Failure Analysis and Prevention, Volume 12, Issue 6 (2012), pp 670-682, also Digital Object Identifier (DOI) September 13, 2012, DOI 10.1007/s11668-012-9606-9.
- “Investigation of the Effects of Catalyst Loading and Gas Flow Rate on Polymer Electrolyte Membrane (PEM) Fuel Cell Performance and Degradation,” Anthony C. Okafor and Hector-Martin Mogbo, ASME Journal of Fuel Cell Science and Technology, February 2012, Vol. 9/011006-1- 011006-13.
- “Design and Analysis of Adhesively Bonded Thick Composite Patch Repair of Corrosion Grind-Out and Cracks on 2024-T3 Clad Aluminum Aging Aircraft Structures,” A. Chukwujekwu Okafor, and Hari Bhogapurapu, Composite Structures, Vol. 76, (2006), pp 138-150.
- “Design, Analysis and Performance of Adhesively Bonded Composite Patch Repair of Cracked Aluminum Aircraft Panels,” A. C. Okafor, Navdeep Singh, U. E. Enemuoh, and S. V. Rao, Composite Structures, Vol. 71, (2005), pp 258-270.
- “Determination of Optimal Ultrasonic Pulse Repetition Rate Frequency for Damage Detection in Composites and Aluminum Plates Using Neural Networks,” A. Chukwujekwu Okafor, and Amitabha Dutta, Nondestructive Testing and Evaluation International Journal, Vol 34/7, pp 469- 481, July 2001.
- “Detection and Characterization of High-velocity Impact damage in Advanced Composite Plates Using Multi-sensing Techniques,” A. C. Okafor, A. W. Otieno, A. Dutta, and V. S. Rao, Composite Structures, Vol. 54/2-3, (2001), pp 289-297.
- “An Approach for Development of Damage-Free Drilling of Carbon Fiber Reinforced Thermosets,” E. Ugo Enemuoh, A. Sherif El-Gizawy, and A. Chukwujekwu Okafor, International Journal of Machine Tools and Manufacture 41 (2001), pp 1795-1814.
- “Derivation of Machine Tool Error Models and Error Compensation Procedure for 3 Axes Vertical Machining Center using Rigid Body Kinematics,” A. C. Okafor, Yalcin M. Ertekin, International Journal of Machine Tools and Manufacture, 40 (2000), pp 1199-1213.
- "Vertical Machining Center Accuracy Characterization using Laser Interferometer Part 1: Linear Positional Errors,” A. Chukwujekwu Okafor, Yalcin Ertekin, Journal of Material Processing Technology, volume 105/3 (2000), pp 394-406.
- "Vertical Machining Center Accuracy Characterization using Laser Interferometer Part 2: Angular Errors,” A. Chukwujekwu Okafor, Yalcin Ertekin, Journal of Materials Processing Technology, Volume 105/3 (2000), pp 407-420.
- “Structural Damage Detection in Beams by Wavelet Transforms,” A. Chukwujekwu Okafor and A. Dutta, Smart Materials and Structures Journal, Volume 9/6 (2000), pp 906-917.
- “Neural Network Based Sensor Fusion for On-Line Prediction of Delamination and Surface Roughness in Drilling AS4/PEEK Composites,” Ugo E. Enemuoh, A. Sherif El-Gizawy, A. Chukwujekwu Okafor, 1999 Transactions of the North American Manufacturing Research Institution of SME, Vol. XXVII, 1999, pp 263 - 268.
- “Monitoring and Predicting Surface Roughness and Bore Tolerance in End Milling,” Okafor, A. C., Book Chapter 18 in Computer-Aided Maintenance: Methodology and Practices, Edited by Dr. Jay Lee and Dr. Ben Wang, Kluwer Academic Publishers, 1999, ISBN 0-412-629-704.
Follow Intelligent Systems Center